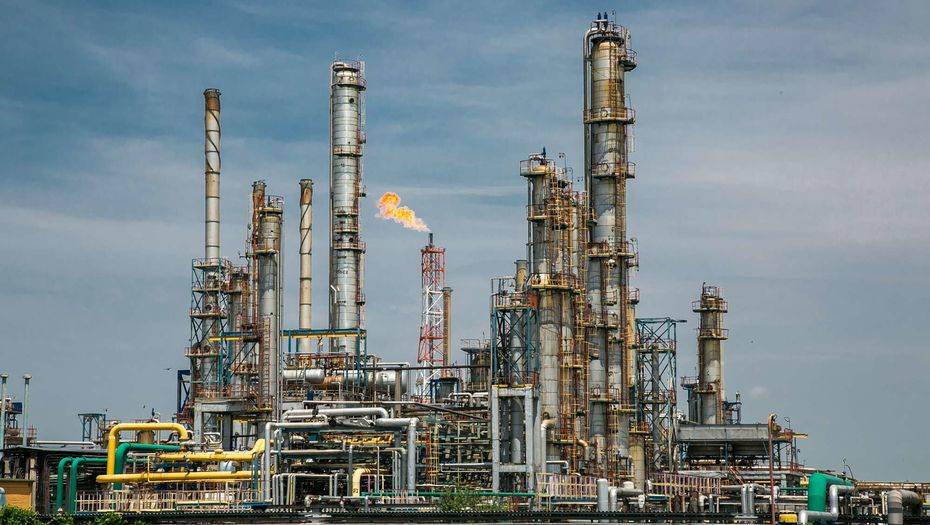
В партнёрском проекте с компанией KMG International рассказываем, как работает нефтеперерабатывающий завод Petromidia.
Группа журналистов и операторов стоит на берегу терминала Midia Marina Terminal в Чёрном море, наблюдая, как огромный танкер с греческим флагом на корме загружают нефтепродуктами румынского производства. Пришвартовавшиеся на девятом причале танкер и небольшая баржа образуют мини-залив, в котором внезапно показывается настоящий дельфин. Этих умных морских обитателей здесь водится много, они даже стали символом города Нэводарь в уезде Констанца, который известен не только популярным среди местных и туристов курортом Мамайя, но и построенным здесь ещё в 1975 году крупнейшим нефтеперерабатывающим заводом в Румынии – Petromidia, частью инфраструктуры которого и является морской терминал.
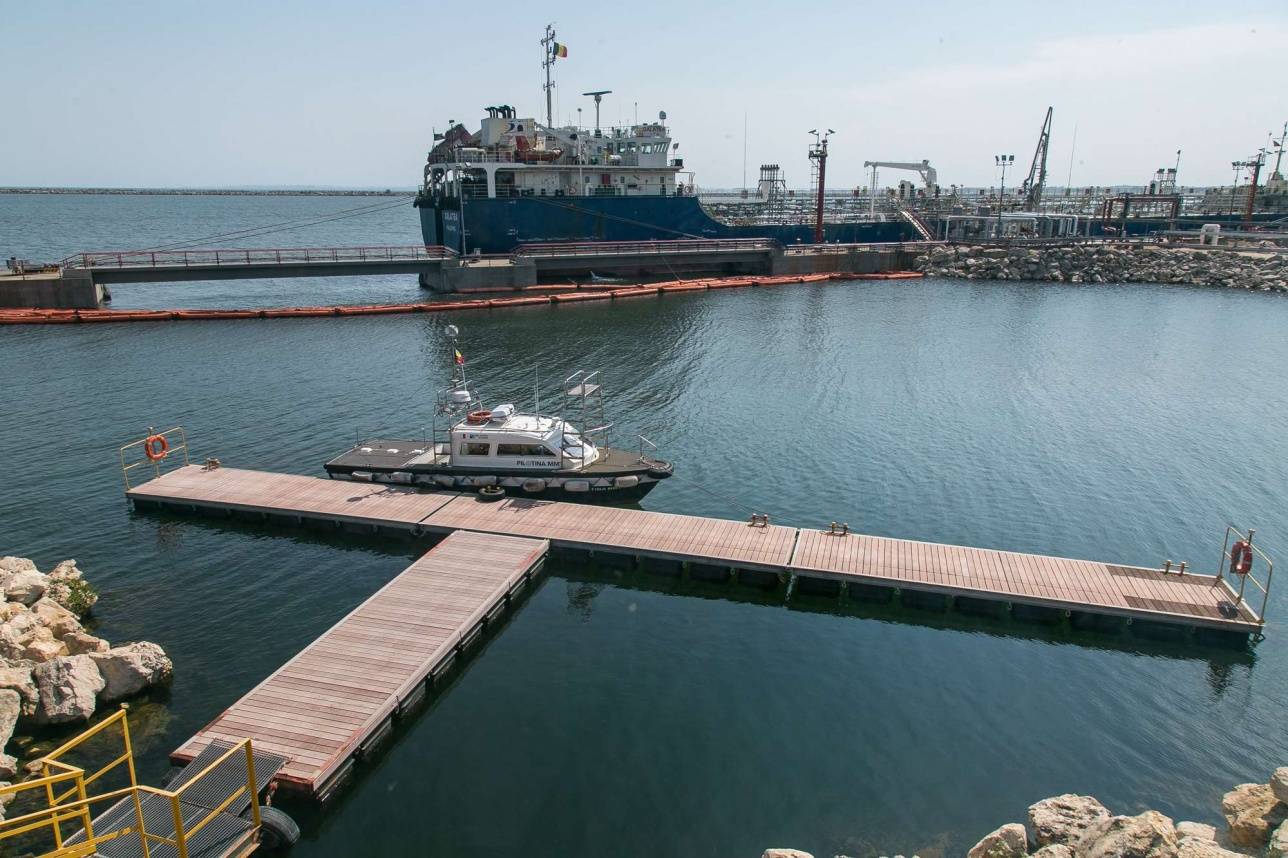
Защита окружающей среды и биоразнообразие
Близость объекта по переработке и транспортировке нефти к Чёрному морю с его флорой и фауной, а также тысячами отдыхающих на прибрежных пляжах туристов, кажется, не удивляет никого, кроме группы казахстанских журналистов.
Представители Petromidia говорят, что на заводе особенно трепетно относятся к экологии. Предприятие окружено населёнными пунктами, один из которых – популярный курорт Мамайя, поэтому операторы круглосуточно следят за уровнем выбросов парниковых газов, которых здесь практически не бывает. В 2017 году индекс энергоёмкости "Соломон" снизился на 15 баллов по сравнению с 2012 годом (99,96 в сравнении с 114,9), а это означает, что показатель энергоэффективности производства постоянно улучшается. Также строго соблюдаются все нормативы по утилизации отходов. Всё это говорит о современности и экологичности завода Petromidia.
На территории самого завода есть два искусственных водоёма, которые стали домом для более чем 4 тысяч видов животных и растений. Благодаря трёхэтапному процессу очистки воды, проводимому на Petromidia, вода используется повторно, не представляя опасности для биоразнообразия. Установка системы очистки сточных вод Rompetrol Rafinare, на которой перерабатываются заводские сточные воды и сточные воды города Нэводарь, позволила без вреда для окружающей среды сбрасывать воду в Чёрное море после соответствующей механико-химической, биологической и природной очистки в искусственных водоёмах на территории завода.
Получается, что завод не только не вредит городу, но и помогает очищать окружающую среду вокруг города Нэводарь.
Модернизация, вдохнувшая в производство новую жизнь
Petromidia – это платформа, объединяющая крупнейший нефтеперерабатывающий завод и единственный нефтехимический комплекс в Румынии. Petromidia – связующее звено компании KMG International между операционными подразделениями трейдинга и поставок, а также сбыта топлива на сеть автозаправочных станций под брендом Rompetrol в Румынии, Молдавии, Болгарии и Грузии.
Шесть лет назад Petromidia модернизировали благодаря инвестициям мажоритарного акционера АО "НК "КазМунайГаз": теперь завод не только самый крупный в Румынии, но и один из самых технологически продвинутых в Восточной Европе. Индекс сложности НПЗ по Нельсону – 10,5; предприятие производит топливо исключительно стандарта Euro 5.
Производство Petromidia на 86% состоит из светлых нефтепродуктов, а модернизированная установка каталитического крекинга входит в десятку лучших в мире по версии производителя подобных установок.
Предприятие полностью соответствует стандартам экологического производства BAT (наилучшие доступные технологии) – это первый румынский завод, работающий по экологическим нормам ЕС и стандартам качества топлива.
Читайте также:
К4, АИ и октановое число: 8 актуальных вопросов о качестве бензина в КазахстанеВ офисе при въезде на завод на всю стену фойе висит панорамная карта завода со всеми установками нефтеперерабатывающего и нефтехимического комплексов. Директор департамента инжиниринга завода Petromidia Кристиан Болохан, показывая на карту, говорит, что
в рамках модернизации Petromidia с 2008 по 2012 год компания Rompetrol Rafinare построила и модернизировала девять промышленных объектов, благодаря чему мощность завода увеличилась с 3,8 до 5 млн тонн сырой нефти в год.
Модернизация подразумевала строительство пяти новых установок:
- установки мягкого гидрокрекинга;
- установки производства серы;
- установки производства водорода;
- азотной установки;
- новой факельной системы.
И усовершенствование четырёх существующих установок:
- модернизация установки каталитического крекинга;
- реконструкция установки Клауса;
- переоборудование установки гидроочистки вакуумного газойля в установку гидроочистки дизельного топлива;
- реконструкция установки очистки аминами.
Важной частью модернизации стала реконструкция установки каталитического крекинга – она предназначена для глубокой переработки фракций, что позволяет получить бензин с максимально высоким октановым числом.
Так удалось увеличить производство дизельного топлива от 1,5 до 2,8 млн тонн, поднять уровень производства светлой продукции до 86%, при этом себестоимость переработки сырой нефти снизилась за период с 2012 по 2017 годы с 28 до 16 долларов на тонну, что было одной из важных целей группы KMG International.
В общем же модернизация позволила в 2017 году достичь рекордных показателей в 16 тысяч 760 тонн переработки сырья в день. В Европе действуют всего несколько заводов с такими внушительными показателями.Нефтеперерабатывающий и нефтехимический комплексы полностью интегрированы, располагаются на территории по разным сторонам дороги, которая ведёт к Центру управления или Сontrol centre, как его здесь называют. На нефтехимической половине три основных установки: для производства полипропилена и полиэтилена, полиэтилена высокой и низкой плотности.
Установку по производству полиэтилена высокой плотности запустили совсем недавно – это ответ на тенденции рынка: по словам Куаныша Досмуратова, руководителя центра компетенции Petromidia, в мире растёт спрос на нефтехимию. У завода уже есть клиенты из Болгарии и Турции, а эксперты прогнозируют рост спроса в Европе и в мире уже в следующем году.
На установке полипропилена недавно усовершенствовали катализатор, благодаря чему теперь установка производит более высококачественную и безопасную для людей продукцию и, соответственно, более высокомаржинальную.
Центр дистанционного управления
"Вы заметили, что на заводе почти нет людей?" – спрашивает журналистов Куаныш Досмуратов. "Это потому, что всё управление заводом вынесено на DCS (распределённая система управления), и все установки регулируются из двух комнат на втором и третьем этажах центра управления".
Визуально центр управления делится на две части – инженерную и операционную. Это один из немногих заводов в мире, где эти две функции находятся физически рядом, в одном здании. Здесь это нужно для более эффективной и оперативной коммуникации между отделами в целях оптимизации и диджитализации производства. В фойе висят постеры с описанием программы внутренней оптимизации "Дельфин", цель которой – постоянное улучшение. Каждое подразделение на заводе всё время находится в поиске решений, которые бы помогли сделать его часть работы эффективнее, экологичнее и технологичнее. Здесь искренне верят, что всегда есть куда расти и поэтому рассматривают все инициативы сотрудников разного уровня.
По дороге к комнатам управления входим в диспетчерскую. На нескольких экранах отображаются показатели по выбросам серы: датчики фиксируют 0,00001% (одну стотысячную процента) – что вполне может быть и погрешностью. То есть вредные выбросы в атмосферу практически сведены к нулю, а контроль за их уровнем осуществляется в ежесекундном режиме.
На территории завода не горит ни один из трёх факелов по выбросам серы, а в воздухе не чувствуется ничего кроме дыхания морского бриза. Все серные газы улавливаются и перерабатываются.
Операторы разделены по секциям и этапам процессов на установках, за которыми они следят. Параметры на установках задаются операторами вручную. У них есть камера, чтобы видеть установку в реальном времени, и рация для переговоров со специалистами, которые работают на местах. Работа ведётся круглосуточно, смена одного оператора длится восемь часов. В одной комнате сидят сотрудники предпенсионного возраста и молодые специалисты, которые перенимают опыт.
Здесь всё технологично и надёжно, но Центр компетенций, которым руководит Куаныш Досмуратов, уже начал внедрение следующего технологического уровня управления установками на заводе, который называется Advanced Process Control. APC автоматизирует конфигурации и позволяет добиваться наибольшей эффективности, задавая оптимальные параметры работы установки.
Пока Advanced Process Control действует только на одной установке в пилотном режиме, но планируется, что к 2020 году система будет установлена на всех объектах завода. Экономическая выгода от работы экспериментальной установки уже составила 1,2 млн долларов за первый год тестирования.
Морской терминал в 9 километрах от берега
Сотрудники завода неоднократно подчёркивали уникальное географическое расположение комплекса на берегу Чёрного моря, благодаря которому у завода есть собственный морской терминал для принятия нефти. Пропускная способность терминала – 15 млн тонн в год. Находится он в море, в девяти километрах от берега: нам не удалось туда попасть из-за сильных волн. На этом выносном причале в открытом море компания может принимать суда грузоподъёмностью до 140 тысяч тонн.
Есть несколько причалов и на берегу: 9A, 9B и 9С. На причале 9С, например, грузят только баржи грузоподъёмностью до 3 тысяч тонн, которые доставляют грузы бренда Rompetrol в Болгарию, Молдавию или на экспорт в Сербию. 9А и 9B используются для экспорта нефтепродуктов с завода на больших танкерах до 24 тысяч тонн. На причале 9А ещё есть возможность разгружать этилен для нефтехимии и экспортировать LPG – это единственный терминал такого рода в Чёрном море. Проектная мощность всех трёх причалов – 3 млн тонн в год, но пока максимальные показатели достигли 2 млн тонн, потому что растут объёмы перевозок нефтепродуктов автоцистернами и на железнодорожных путях на территории Румынии и в соседних странах, где представлена розничная сеть автозаправок Rompetrol.
В терминале есть операторская, из которой специалисты следят за всеми погрузочными и разгрузочными операциями от момента присоединения шлангов до момента опломбирования танкеров. Здесь же следят за давлением в трубах, температурой, плотностью продукта и объёмами загрузок и отгрузок топлива между танкерами и резервуарами на заводе. Помимо автоматизированной системы за объёмами и качественными показателями погрузок следят независимые инспекторы, нанятые той или иной стороной сделки. Танкеры пломбируются.
Чтобы загрузить танкер объёмом 24 тысячи тонн, требуется примерно 2,5 дня: средний погрузочный объём – 500 тонн в час.
Кроме морских причалов Midia Marine Terminal оперирует и наземным нефтехранилищем, где загружаются автоцистерны компании Rompetrol и другие клиенты компании, которые перевозят топливо наземными путями. Здесь всё автоматизировано: у каждого водителя есть электронная карта, которая даёт ему доступ в нефтехранилище. Погрузка автоцистерн осуществляется через автоматизированную систему TAS – водителю на месте нужно только распределить виды топлива по отсекам автоцистерны на электронном терминале и вовремя заехать на выделенную для него колонку (номер автомобиля отображается на электронном табло).
Отсюда дизель и бензин распространяются по партнёрским и собственным сетям автозаправочных станций, которые находятся во всех уголках Румынии и Молдавии. Ритейл и пункты продаж топлива Rompetrol – это следующая и заключительная стадия бизнес-цепочки. Расширение собственной сети автозаправок и повышение доли высокомаржинальных продаж топлива "с пистолета" – направление, на которое компания намерена сделать ставку в ближайшие годы.
Недавно мы писали о пяти причинах путешествовать налегке: это удобно, безопасно и экономично-
1❓"Треть территории Казахстана сейсмически опасна". Учёный о вероятности новых землетрясений
-
3933
-
7
-
55
-
-
2🌡Прогноз погоды на 10 апреля: дождь, гроза и сильный ветер ожидаются на западе, востоке и севере Казахстана
-
2780
-
0
-
7
-
-
3❗️От рядового агронома до партийного лидера. Токаев выразил соболезнования родным Веры Сидоровой
-
2634
-
0
-
100
-
-
4🔖 Токаев поручил министру транспорта увеличить количество внутренних и международных авиарейсов
-
2333
-
1
-
106
-
-
5⚠️ Доброе утро! Предлагаем обзор главных новостей за 9 апреля
-
2465
-
0
-
7
-
-
6🥊Балауса Муздиман: Теперь хочу перебраться в США, чемпионский бой уже запланирован
-
2384
-
0
-
27
-
-
7⚡️Водный кодекс Казахстана подписал Токаев
-
2363
-
0
-
105
-
-
8⚡️Токаев провёл совещание в связи с изменением ситуации на мировых рынках
-
2354
-
7
-
110
-
-
9🌡Прогноз погоды на 11 апреля: пыльная буря ожидается в Астане и местами на севере Казахстана
-
2191
-
1
-
0
-
-
10🇺🇸СМИ: Пошлина США на китайские товары составит 145%
-
2070
-
2
-
17
-