
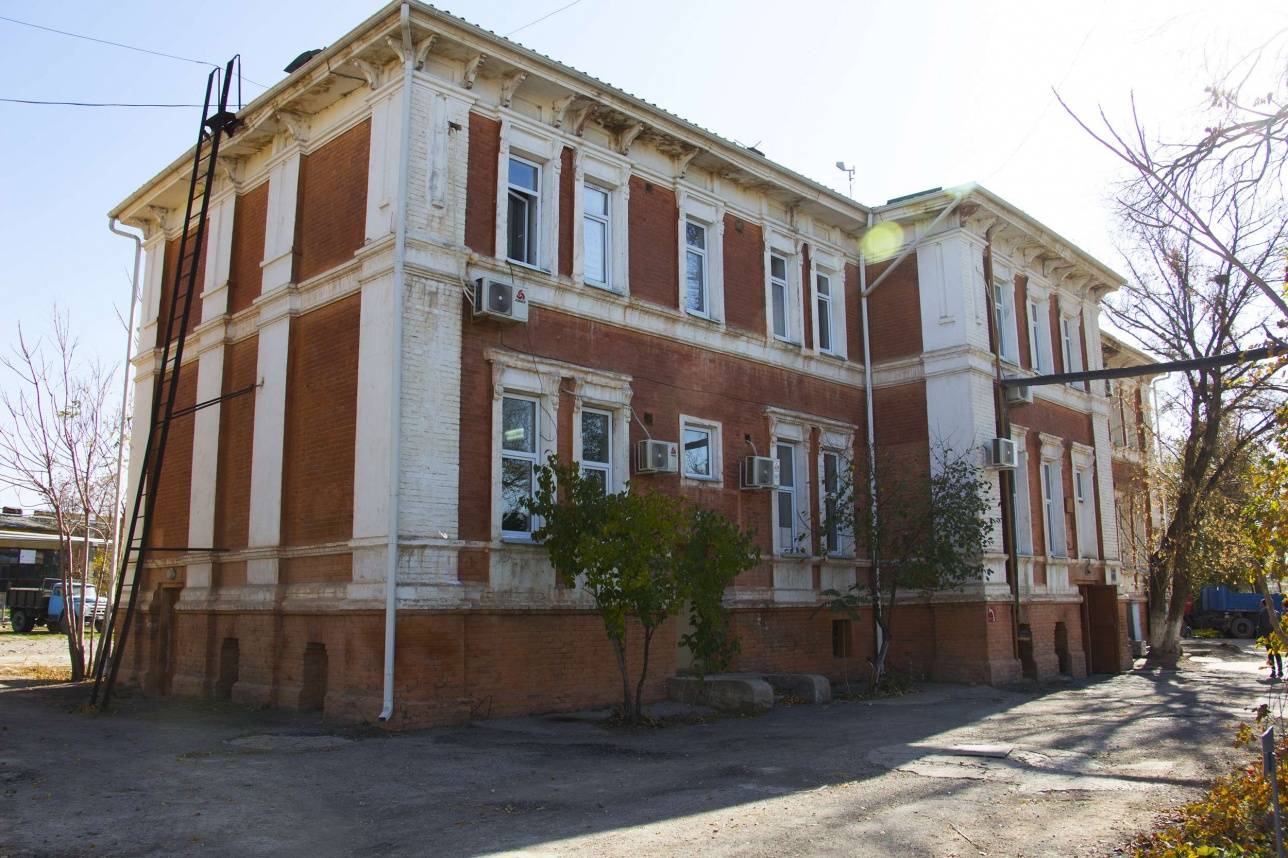
В 1882 году к Н. И. Иванову обратился немецкий химик Вильгельм Пфафф с предложением организовать производство сантонина из дикого растения дарман, которое растёт неподалёку от Шымкента в долине реки Арысь. Меньше чем за год Иванов и Савинников перевезли в город химические агрегаты из Германии и начали строительство помещений завода. А ещё через год, в 1884-м, предприятие уже работало.
Читайте также:
От целебных трав до биотехнологий: Полная история казахстанской фармации
Спустя ещё несколько лет на территории завода появился дом купцов, где они жили и, предположительно, проводили рабочие планёрки. Здание до сих пор в отличном состоянии.
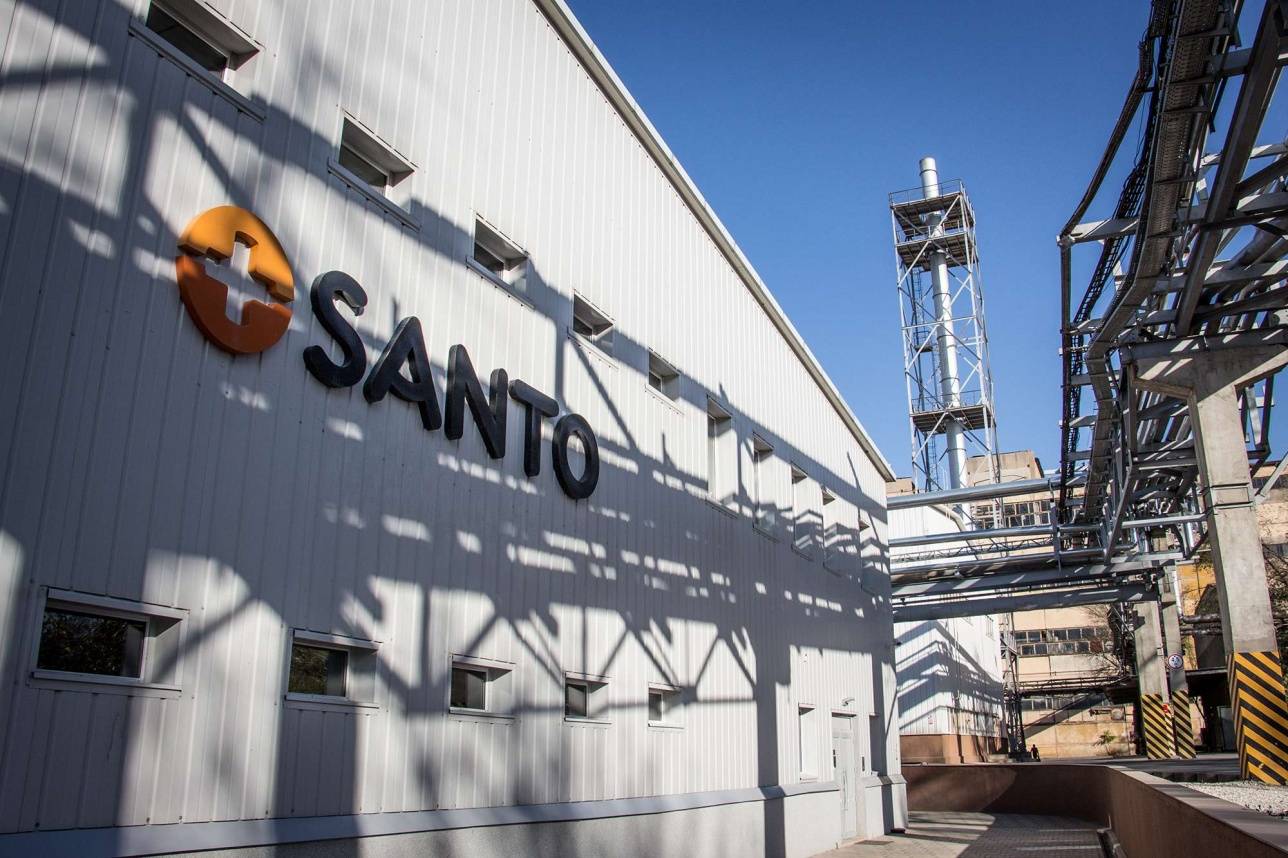
Сегодня Шымкентский химико-фармацевтический завод преобразовался в компанию SANTO. Это современное производство, построенное в соответствии с международным стандартом качества GMP и которое выпускает свыше трети отечественных лекарств.
Всего на заводе производится более 200 генерических препаратов. А производственные мощности компании позволяют ежегодно производить 600 миллионов таблеток, 300 миллионов ампул, 6 миллионов инфузий, 40 миллионов флаконов антибиотиков и 26 миллионов флаконов сиропов.
Цех по производству инъекционных растворов и инфузий
Здесь производят препараты в ампулах (для внутривенного и внутримышечного применения) и препараты кровезаменители (для внутривенного применения). Цех состоит из 4 инъекционных линий и 2 линий производства инфузионных растворов. Разработка проекта была поручена итальянской компании, чтобы выпускаемая продукция соответствовала стандартам GMP.
GMP (Good Manufacturing Practice) – правила и требования к производству и контролю качества лекарственных средств. Надлежащая производственная практика GMP – это международный стандарт качества, согласно которому осуществляется производство лекарственных средств в странах с жёсткой регуляторной системой, таких как страны ЕС, США, Япония. Мировая история GMP стандартов берёт своё начало с 1963 г. в США, где группой учёных были разработаны специальные правила для регламентирования условий качественного и безопасного производства лекарственных препаратов. В 1969 году была принята резолюция ВОЗ, которая предписывала применять правила GMP WHO всем странам. С 1 января 2018 года требования GMP будут обязательными при производстве лекарственных средств в Казахстане. Практически вся продукция компании SANTO уже соответствует этим стандартам.
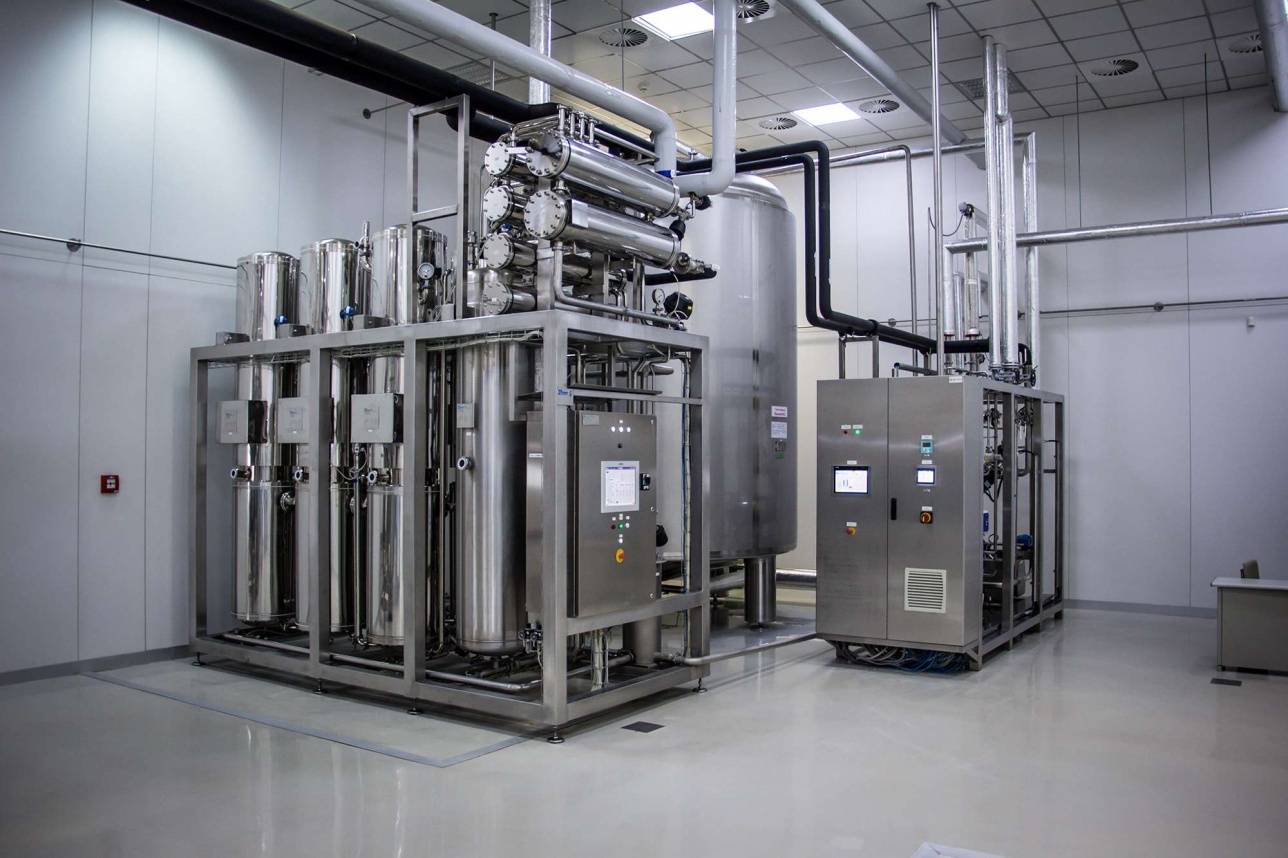
Процесс производства начинается с подготовки пара, воздуха и воды, которые проходят несколько этапов очистки. Электронная система следит за тем, чтобы все характеристики соответствовали требованиям. Например, если после очистки у воды превышен такой показатель, как электропроводность, она автоматически уходит в слив и не допускается до производства.
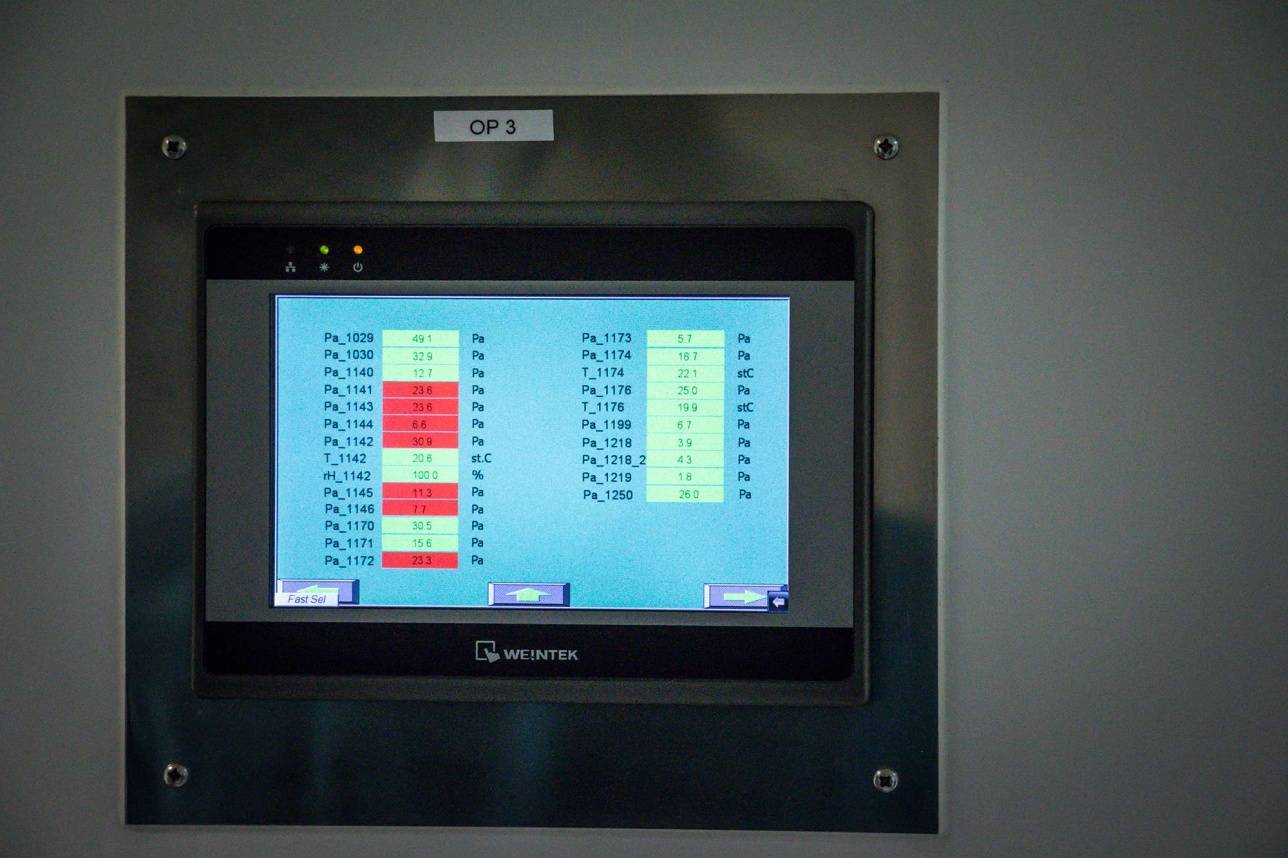
По всему цеху в стены вмонтированы информационные электронные панели. Они отображают температуру, влажность, давление в помещении и количество частиц, содержащееся в воздухе в производственном помещении и внутри машины. Информация отображается в трёх цветах – красный, жёлтый, зелёный. Если на панели горит красный прямоугольник (с указанным показателем и номером помещения), это значит, что показатель не соответствует норме. Жёлтый означает «уровень тревоги» и производственные процессы запрещены. Зелёный цвет говорит о том, что все показатели в норме.
Стерильность – это главное слово, которое ассоциируется с производством лекарств. Весь цех поделён на разные зоны по классу чистоты: А, В, С и D. В каждой ведётся строгий контроль за поддержанием уровня стерильности. Например, если вы захотите попасть из зоны D в зону C, вам необходимо пройти через специальный коридор (санитарный пропускник). Электронная система не позволит открыть две двери одновременно, чтобы между зонами не образовался свободный воздушный поток. Чтобы пройти в классифицируемую зону, необходимо переодеться и провести дезинфекцию рук согласно утвержденным процедурам. Если сотруднику необходимо перемещаться между зонами 10 раз за рабочий день, он переоденется 10 раз.
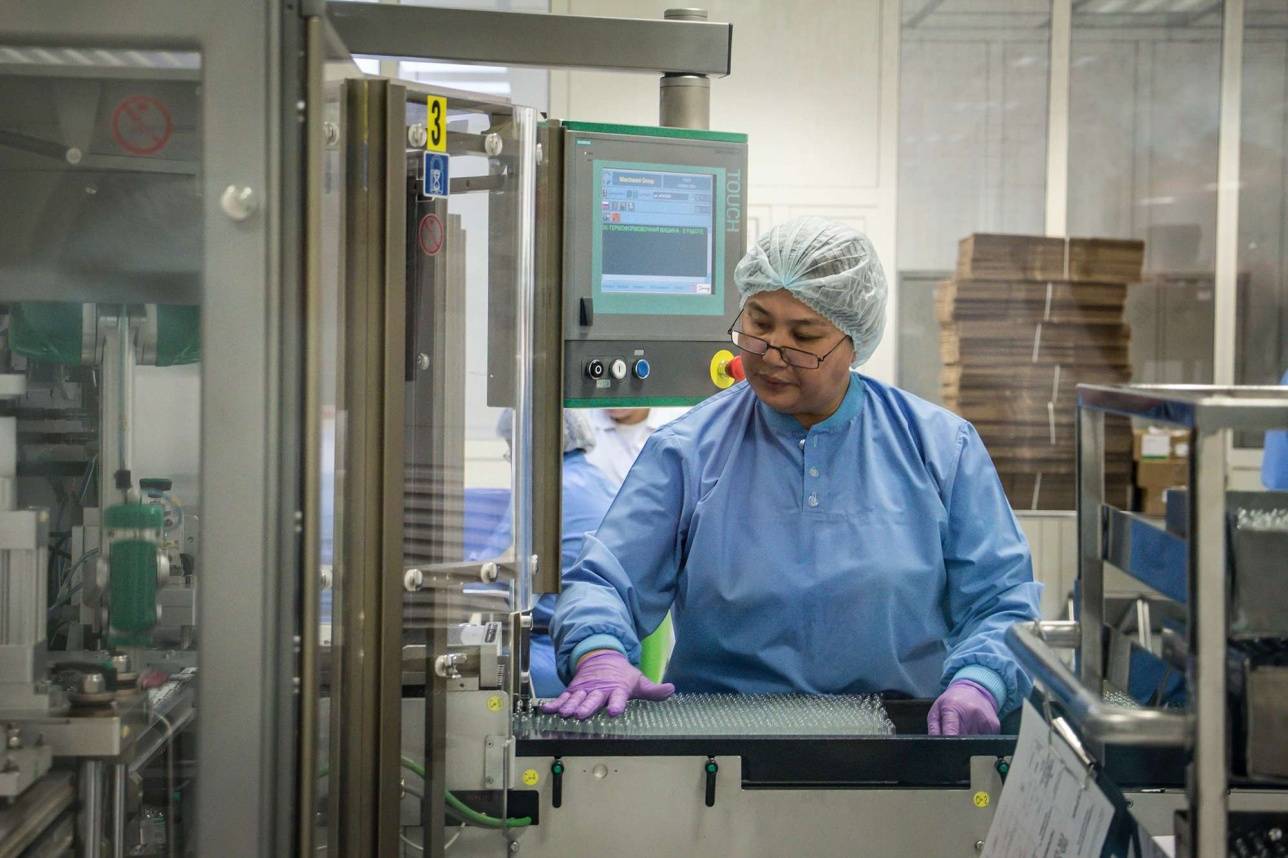
В зоны повышенной стерильности допускаются только специалисты, имеющие необходимую квалификацию, – стандарты работы настолько строгие, что они регламентируют даже скорость ходьбы по помещению и динамику движений руками.
Производственный процесс состоит из трёх этапов: стерилизация ампул, розлив и запайку препарата и финишную стерилизацию препарата с раствором. Розлив и запайка ампул с продуктом интересовали нас больше всего – как удаётся создать цельную округлую ампулу с жидкостью внутри? Ответ в этом видео:
Процесс запаивания ампул происходит в двух фазах. Во время первой фазы происходит предварительный нагрев ампул, в это время пламя направлено на верхнюю часть ампул, в то время как сама ампула вращается. Во время второй фазы стекло плавится, вращающиеся ампулы запаиваются и щипцами убирается верхняя часть. После этого получаем герметично запаянную ампулу.
Второе главное слово на заводе SANTO – контроль. Каждая ампула проходит визуальную проверку. И если хоть на одной ампуле будет замечена микротрещина или пылинка – это будет являться основанием для остановки линии и тотальной проверки. Если же визуальная проверка пройдена успешно, то ампулы отправляются на этикетировку и упаковку.
Препарат готов к выпуску в реализацию через 15 дней. Столько времени нужно, чтобы его проверила независимая лаборатория и выдала сертификат.
Цех асептической рассыпки порошков антибиотиков
Открытие цеха состоялось 24 мая 2016 года. С этого момента порошки антибиотиков производятся отдельно, как это требует стандарт GMP на двух модернизированных линиях – это линия цефалоспоринов и линия пенемов и других антибиотиков. В цехе производят 14 наименований на линии цефалоспоринов и 7 наименований на линии пенемов и других антибиотиков.
Здесь весь цикл производства проходит в условиях абсолютной стерильности. Первый и самый важный этап – подготовка флаконов. Она состоит из восьми этапов, последний из которых – стерилизация при температуре не менее 300 градусов. Подготовленные флаконы передаются на стадию рассыпки порошков антибиотиков.
Затем во флаконы рассыпаются порошки, и происходит процесс закупорки. Рассыпка антибиотиков производится в асептических условиях, где постоянно контролируются параметры температуры, влажности, частиц воздуха. После этого флаконы попадают в зону визуального осмотра, где проводится контроль на механические включения, качество стекла, качество закатки и наличие субстанции во флаконе.
Все процессы производства снимаются на камеру. Персонал, занимающийся просмотром, каждый час меняется другим.
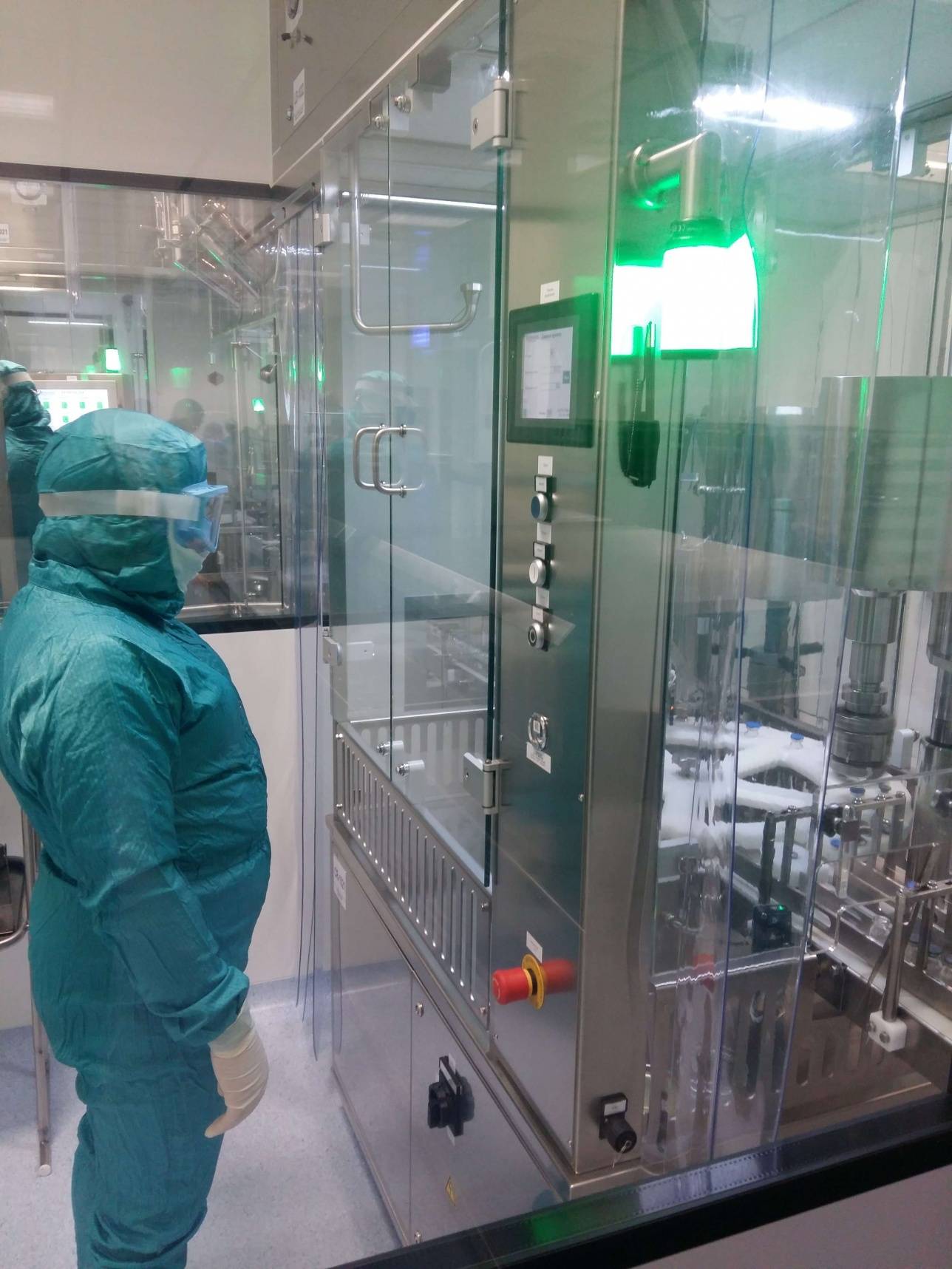
Затем препарат попадает в зону упаковки. Флаконы упаковывают в маленькие коробочки для розничной реализации в аптеках и такие большие поддоны для поставок в больницы. Кстати, компания SANTO покрывает 15% потребности госзаказа в медикаментах.
Далее готовая продукция отправляется на склад со статусом «карантин», а отобранные с каждой серии образцы проходят полностью физико-химический и микробиологический анализ, по положительным результатам которого продукция снимается с карантина и отправляется в реализацию.
Цех твёрдых пероральных лекарственных средств
Если проще – цех по производству таблеток и порошков. Он самый новый и построен по всем требованиям GMP. Tехническое открытие состоялось 8 сентября этого года. В таблеточный цех было инвестировано 13,5 млн долларов. Для работы в нём персонал обучен на лучших производственных площадках Polpharma.
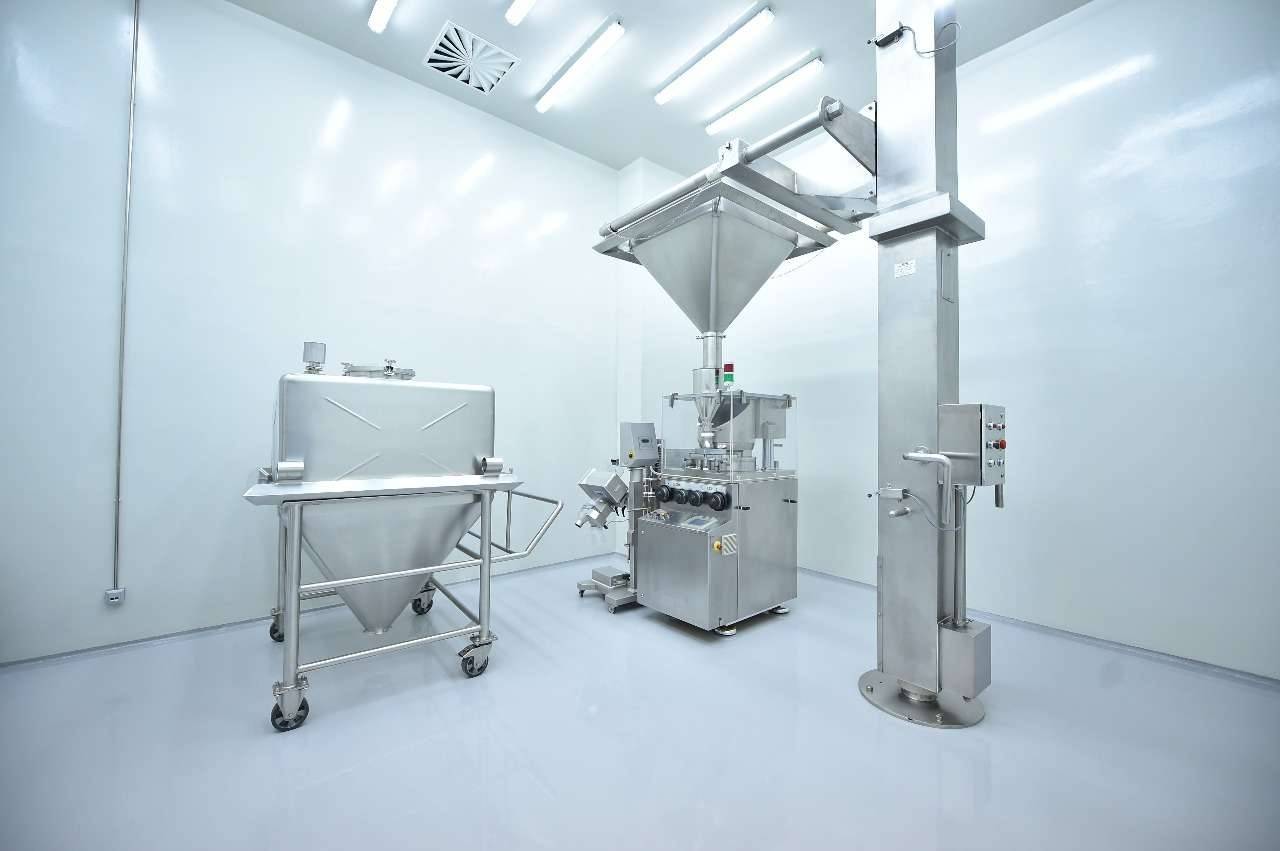
Подготовленные компоненты для производства таблеток/порошков с помощью пневмотранспорта загружаются в мобильный бин. Затем мобильный бин с помощью подъёмной колонны устанавливается на биновый смеситель, предназначенный для смешивания компонентов. Специалист задаёт необходимые время и скорость смешивания. Смешанные компоненты в мобильном бине транспортируются на таблеточный пресс для таблетирования и получения таблеток.
Далее таблетки поступают на упаковочную линию. При упаковке таблеток происходит автоматический контроль процесса. В случае, если в конвалюте не хватает хоть одной таблетки, то она автоматически удаляется с линии. А остальные конвалюты с таблетками перемещаются на вторичную упаковку в пачки и далее на групповую упаковку в коробки.
Смешанные компоненты для получения порошков поступают на автоматическую машину для упаковки в саше-пакеты.
Научно-исследовательский институт
НИИЦ при предприятии SANTO – один из лучших в стране. Здесь в прямом смысле слова изобретают лекарства. Последнее изобретение – БАД "Мукалсан" на основе натуральных ингредиентов. Это напиток, по вкусу напоминающий «Буратино», а по свойствам является правопреемником знаменитого мукалтина.
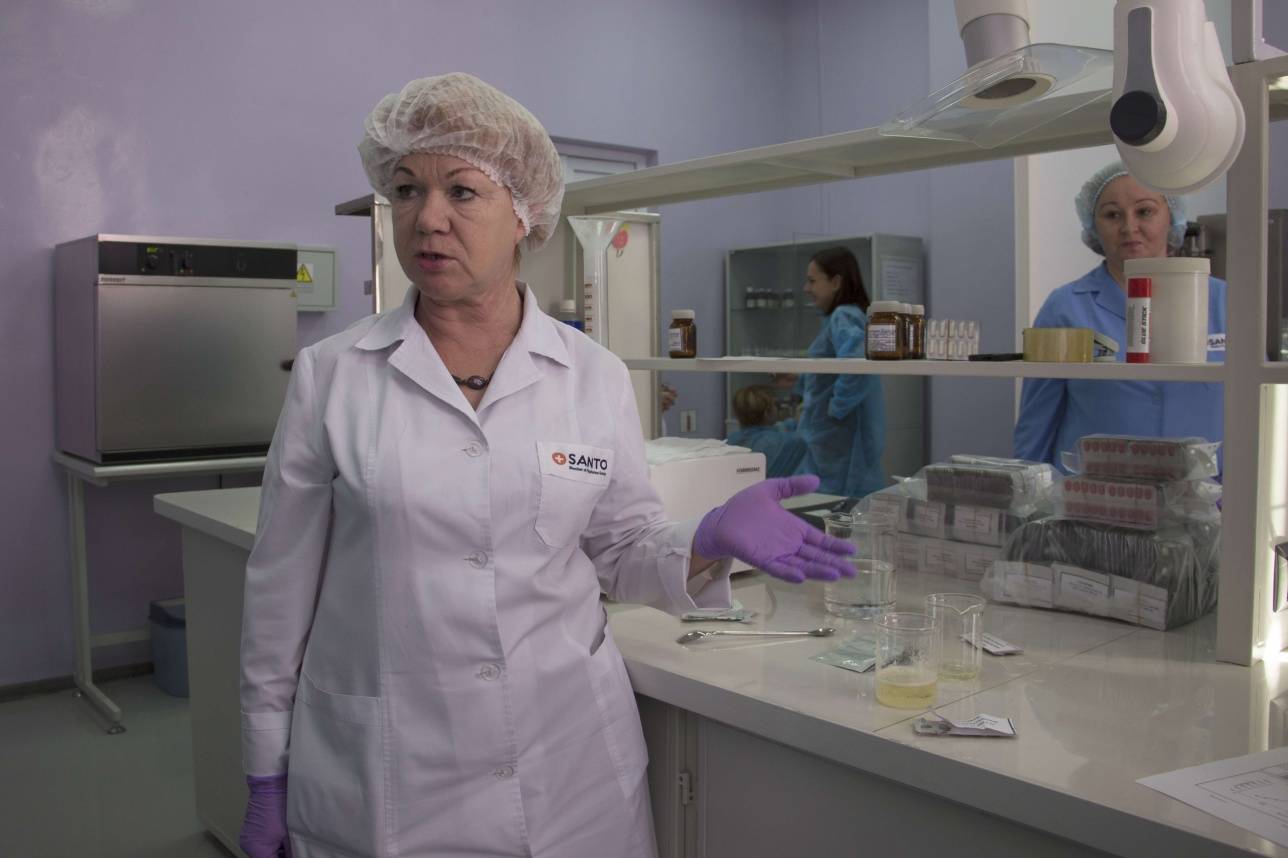
Завод SANTO – крупнейший иностранный инвестиционный проект. В него уже вложено более 100 млн долларов, и это только начало. А это значит, что скоро появятся новые производственные мощности, новые препараты и у нас будет повод вернуться сюда снова.
Партнерский материал
-
1📚 Как создают школьные учебники и почему они не всегда соответствуют ожиданиям
-
2764
-
4
-
21
-
-
2🏫 Смена электронных дневников в школах Казахстана: поиск лучших решений или борьба за рынок?
-
2965
-
4
-
28
-
-
3⚠️ Доброе утро! Предлагаем обзор главных новостей за 13 ноября
-
2626
-
0
-
5
-
-
4❌ В горах Алматы объявили лавинную опасность в ближайшие дни
-
2663
-
0
-
14
-
-
5📱 Мошенники выманили 10 млн тенге у родителей школьников, прочитав их чат в мессенджере
-
2466
-
0
-
31
-
-
6🐍 Живых змей обнаружили в посылке с детскими игрушками в Германии
-
2338
-
1
-
25
-
-
7🛍 До 20 долларов на всё: акции Amazon достигли максимума после объявления о запуске сервиса-конкурента Temu
-
2260
-
0
-
8
-
-
8🛸 Конгресс США вновь пытается раскрыть правду об НЛО
-
2144
-
0
-
30
-
-
9⚽️ 14 ноября Казахстан сыграет с Австрией в Лиге Наций
-
2155
-
0
-
11
-
-
10🍌🥝 Более 12% казахстанцев не могут обеспечить детям свежие фрукты и овощи ежедневно
-
2073
-
12
-
38
-