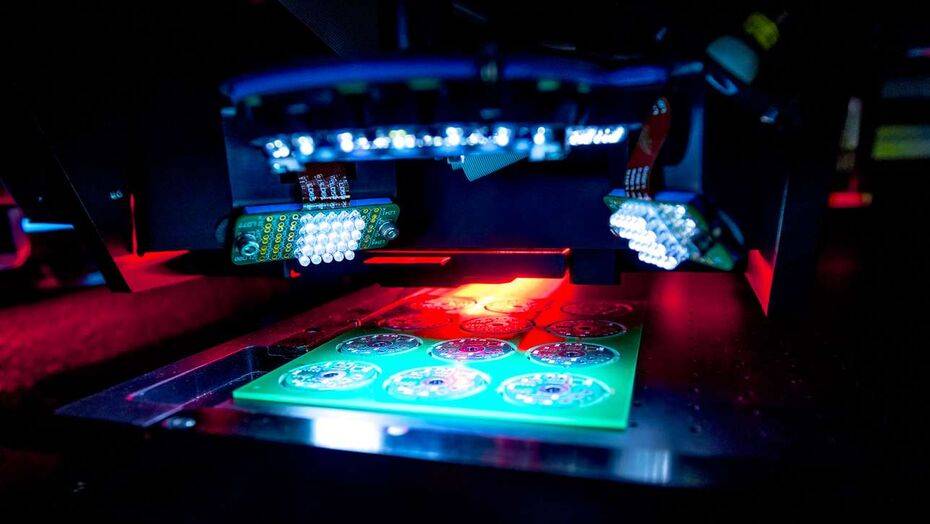
Предприятия казахстанского оборонно-промышленного комплекса не закрывались во время чрезвычайного положения в Казахстане и продолжали работать в условиях карантина. В их числе – АО "Завод им. С.М. Кирова". Он расположен в Петропавловске и выполняет государственный оборонный заказ. Основной профиль предприятия – производство различных систем связи для армии и других силовых структур страны. На заводе побывал журналист Григорий Беденко.
Сегодня АО "Завод им. С.М. Кирова", предприятие с более чем 90-летней историей, – это государственная структура, которая входит с состав Национальной компании "Казахстан инжиниринг". Завод расположен в Петропавловске, и его основной профиль – производство систем связи для Министерства обороны РК.
В рамках государственного оборонного заказа предприятие выпускает мобильные комплексы связи, радиостанции тактического звена управления и полигонное оборудование. Также завод выполняет заказы в гражданской сфере. Это приборы автоматики, телемеханики и системы обеспечения безопасности для железнодорожного транспорта, оборудование для предприятий нефтегазового и энергетического комплексов, технические средства цифрового телевещания.
– Производство спецпродукции является основным направлением работы нашего предприятия, – рассказывает Мади Бектенов, директор департамента продаж АО "Завод им. С.М. Кирова". – Мы работаем по нескольким направлениям. По средствам связи основной заказчик – Министерство обороны. Завод выполняет работы по модернизации техники связи, стоящей в настоящее время на вооружении. Есть такая техника, которая уже морально устарела, она не работает. Мы её модернизируем, устанавливаем современное цифровое оборудование связи – передатчики, приёмники. Применяем и собственные разработки, используем зарубежное оборудование. Всё это делается в строгом соответствии с техническим заданием Министерства обороны. Мы работаем также с КНБ, начинаем работу со службой Государственной охраны, с Пограничной службой.
В производстве военных систем связи активно применяются технологии израильского оборонного концерна Elbit Systems. Наиболее массовое серийное изделие такого рода для казахстанских Вооружённых сил – радиостанции тактического звена управления. Это мобильные малогабаритные системы, которые используются личным составов в поле для связи с командованием. Производятся изделия разной мощности и разного исполнения. Продукция поставляется в войска с 2015 года.
Выпускается также аппаратура внутренней связи и коммутации. Эти изделия используются для коммутирования сигнала между различными видами радиостанций внутри определённой командно-штабной машины. Также в рамках гособоронзаказа завод выпускает пульты диспетчерской связи, оказывает услуги по ремонту полигонного оборудования и поставляет комплексы собственной разработки: ротно-тактический комплект, комплект стрельбищного оборудования, танковые директрисы. В настоящее время предприятие уже оснастило около 30 военных полигонов РК.
– С этого года мы планируем заключить контракты с Министерством обороны на поставку и ремонт средств радиоэлектронной разведки и радиоэлектронной борьбы, – рассказывает далее Мади Бектенов. – Это новое для нас направление, новые проекты, которые планируем реализовать совместно с зарубежными партнёрами, среди них белорусская и израильская компании. Также в планах производство комплексов РЭР (радиоэлектронной разведки) и РЭБ (радиоэлектронной борьбы). С этого года мы определены как исполнители данного сегмента гособоронзаказа. Часть объёма переходящая – с этого на следующий год.
Как сообщил Мади Бектенов, в комплексы РЭР и РЭБ входит порядка 7-8 наименований различных изделий. В том числе есть комплекс, который создаётся на базе автомобиля фургонного типа – радиоэлектронной борьбы с беспилотными летательными аппаратами. Этот комплекс в определённой зоне сбивает рабочую частоту, на которой работают БПЛА. Новая система РЭБ получила кодовое название "Гроза".
Завод им. С.М. Кирова выполняет ежегодные работы по модернизации и обслуживанию систем связи, стоящих на вооружении в казахстанской армии. Это мобильная радиостанция средней мощности Р-140 МЦ, радиорелейная станция Р-409 МЦ, радиорелейная станция Р-414 МЦ, мобильная тропосферная радиорелейная станция Р-417, аппаратная П-240 ТМ1, командно-штабная машина Р-142 Н на базе автомобиля КамАЗ, командно-штабная машина Р-145 БМ на базе БТР, а также командно-штабная машина на базе Land Rover.
– У машин, которые мы модернизируем, ресурс зависит от своевременности и полноты обслуживания, – продолжает рассказ Мади Бектенов. – У каждой машины есть свой регламент. Если всё проводить своевременно, то машина может прослужить около 10 лет. Но, к сожалению, опыт показывает, что в войсках не все военнослужащие понимают, как правильно эксплуатировать эти машины. Имеется необходимость проведения дополнительного обучения личного состава по эксплуатации этих систем связи.
По словам Мади Бектенова, неправильное подключение питания, ошибки в подключении антенны или порядка включения оборудования приводят к тому, что комплексы связи выходят из строя раньше срока. Необходимо проводить дополнительный ремонт, а это дополнительные затраты.
– Разумеется, при выполнении работ мы даём гарантию в зависимости от того, как этого требует заказчик. Чаще всего это год. В последнее время требуется двухлетняя гарантия. В прошлом году мы выполнили поставку радиостанций тактического звена управления. На эти изделия мы даём 10 лет гарантии. Этот вопрос мы поднимали перед руководством Министерства обороны – что мы видим необходимость дополнительного обучения личного состава, для того, чтобы оборудование прослужило дольше и всегда была высокая боеготовность, – сообщил Мади Бектенов.
Специалисты завода им. С.М. Кирова разработали три собственных прототипа мобильных систем связи на шасси автомобилей КамАЗ. Это радиостанция средней мощности "Карагай", цифровая радиорелейная станция "Актерек" и тропосферная радиорелейная станция "Ак кайын".
– Создавая эти машины, мы провели опытно-конструкторские работы на основании техзадания Министерства обороны. Техзадание получили в 2015 году. Машины разработаны силами наших специалистов. В качестве прототипа использовалась та техника, которую мы модернизировали ранее. После модернизации все параметры машины улучшаются в разы. Но лишь до того предела, который прописан в технической спецификации. По заданию Минобороны мы предложили свой улучшенный вариант этой техники, то есть по своим параметрам она лучше, чем та техника на конечном этапе, которую мы модернизируем, – продолжил Мади Бектенов. – Машины нашей разработки отличаются улучшенным функционалом, поменяли компоновку оборудования. В целом эти машины более эргономичные, экипажам там работать намного удобнее. При правильной эксплуатации ресурс новых машин значительно больше, чем у той техники, которую мы модернизируем.
Как сообщил Мади Бектенов, машины несколько раз проходили войсковую опытную эксплуатацию в Вооружённых силах. По итогам последних испытаний в целом существенных замечаний не имеется. К примеру, машина "Актерек" полностью соответствует требованиям техзадания, и эта машина готова к принятию на вооружение.
– К сожалению, эти машины мы уже четыре года не можем поставить Министерству обороны, потому что они не приняты на вооружение. Процесс принятия на вооружение осуществляется подведомственной комиссией. Процесс длительный, но он не должен занимать столько времени. Машины изготовлены ещё в 2016 году. С тех пор раза три проводились испытания. Каждый раз мы замечания отрабатывали, доводили технику до соответствия, но результата так и не наблюдается, – завершил рассказ Мади Бектенов.
Как производят высокоточные печатные платы
В 2016 году завод приобрёл высокотехнологичную линию по производству двухсторонних печатных плат V класса точности. Класс точности плат подразумевает под собой толщину проводника. Для каждого класса предусматриваются строго определённые параметры. Минимальный диаметр металлизируемого отверстия, соотношение толщины платы к диаметру отверстия – это главные критерии, по которым присуждается класс точности. Для V класса предусмотрена толщина проводника 0,1 мм и зазор в 0,1 мм. Минимальный диаметр металлизированного отверстия составляет 0,25 мм.
– В 2019 году в декабре мы эту линию доукомплектовали, теперь можем производить уже и многослойные платы, также до V класса точности, – рассказывает инженер-технолог Анна Зарецкая. – Эта линия позволяет изготавливать двухсторонние платы, односторонние и многослойные платы. Всё имеющееся оборудование позволяет изготавливать качественные печатные платы, имеется полный парк оборудования контроля.
Многослойная плата позволяет экономить объём и добиться миниатюризации конечного изделия. V класс сложности – это далеко не предел. В России, например, есть заводы (корпорации "Роскосмос" АО "Океанприбор" и др.) которые выпускают платы VI и VII класса сложности.
– Пожалуй, самая важная часть производства – это электроконтроль, который позволяет оценивать работоспособность уже готовых печатных плат, – продолжает рассказ Анна Зарецкая. – Также у нас имеется полный парк оборудования для определенных химических анализов, с помощью которых можно оценить качество покрытия наших печатных плат. Мы используем все возможные виды финишных покрытий – от самого простого (олово, свинец), до иммерсионного золота, также твёрдое гальваническое золочение концевых печатных контактов. Это все необходимые финишные покрытия, которые создают качественную пайку для поверхностного монтажа. В результате увеличивается срок службы этих изделий. Покрытие защищает от воздействия внешних факторов, чтобы платы не портились.
Технологическая линия по производству печатных палат на заводе им. С.М. Кирова включает в себя оборудование, выпускаемое компаниями разных стран мира. Это Израиль, Швейцария, Италия, Китай, Южная Корея и Германия. Есть также оборудование из США.
– Срок изготовления многослойной печатной платы зависит от сложности и количества слоёв, – рассказывает далее технолог Анна Зарецкая. – Первая операция в производстве четырёхслойной платы – это изготовление внутренних слоёв. Сначала производится сверление базовых отверстий на заготовках, накатывается светочувствительный материал под названием фоторезист. У нас есть самая современная установка (таких даже в РФ и в Европе немного) прямого автоматического экспонирования. Она с помощью источников света и системы зеркал наносит напрямую рисунок – засвечивает на этом материале. Ранее мы использовали фотошаблоны – у нас был целый парк оборудования. Сейчас этот участок отсутствует, фотошаблоны мы не используем. Все происходит напрямую, сокращается трудоёмкость и т.п. После засвечивания рисунка с помощью прямого экспонирования, заготовки передаются на проявление. Когда рисунок проявился, с него снимают фоторезист – внутренние слои готовы.
– Затем самый важный момент – правильно собрать пакет многослойной печатной платы. Он представляет собой некий слоёный пирог. Берутся внутренние слои, дополнительный материал – стеклоткань, фольга, которая будет у нас на внешних слоях, и с помощью специального оборудования контроля все слои складываются в общую заготовку – собираются в пакет. После этого наш пакет отправляется под пресс. При определенном давлении и температуре в течение трёх часов пакет прессуется, то есть всё это превращается в единое целое. В результате мы получаем готовую печатную плату с четырьмя слоями, – рассказывает технолог.
– Далее пресс-форма разбирается, охлаждается, и тут начинается самый интересный и сложный процесс изготовления многослойных печатных плат – это контроль того, что произошло во время прессования изнутри. Зрение человека такого не воспринимает – соответственно, применяется рентгеновская техника. После того как операции по изготовлению внутренних и внешних слоёв завершены, платы проверяют на установке электрического тестирования. Раньше контроль осуществлялся вручную. Это было очень долго. Сейчас я пишу программу как технолог, в электрическую установку, программа загружается, загружается топология рисунка, то есть что выдал конструктор. И, соответственно, уже готовая печатная плата тестируется на этой установке. 2-3 минуты плата средней сложности проходит электрический тест, – сообщила Анна Зарецкая.
Если плата готова к работе, полностью исправна, она отдаётся на поверхностный монтаж, где на ней размещаются радиотехнические элементы. На изготовление четырёхслойной платы в среднем уходит 3-4 дня, если всё работает. За смену завод производит 2,5 квадратных метра двусторонних печатных плат и около двух квадратных метров многослойных плат.
– Мы только начинаем осваивать технологии такого уровня. Для нас многослойные печатные платы – это новый технологический процесс. Мы его осваивали с нуля. В дальнейшем мы будем осваивать 12-слойные платы. А вообще, наше оборудование позволяет производить платы до 16 слоёв, – поделилась планами Анна Зарецкая.
В настоящее время на заводе действуют новые санитарные правила, все сотрудники носят защитные маски.
Редакция благодарит авиакомпанию Fly Arystan и лично Ляззат Набиеву за возможность посетить Петропавловск.
-
1💬 Эксперты прогнозируют снижение базовой ставки к концу 2025 года
-
3212
-
2
-
15
-
-
2🤝 Токаев провёл встречу с Мирзиёевым
-
2712
-
0
-
130
-
-
3💬 В Казахстане появится университет Бишимбаева – правда или ложь? Ответ Миннауки
-
2691
-
8
-
32
-
-
4✈️ 25 тысяч тенге в обе стороны: казахстанская авиакомпания запустила распродажу билетов
-
2734
-
1
-
7
-
-
5💬 Аймагамбетов об охране в школах: Тратятся деньги, но иногда это лишь иллюзия безопасности
-
2704
-
10
-
23
-
-
6❓ Как и когда нужно менять зимнюю резину, рассказали в "КазАвтоЖоле"
-
2582
-
4
-
7
-
-
7🔖 Отравление школьников в Мангистауской области: Минздрав начал расследование, столовую школы опечатали
-
2577
-
1
-
5
-
-
8⚠️ Доброе утро! Предлагаем обзор главных новостей за 3 апреля
-
2437
-
1
-
3
-
-
9🌧 Прогноз погоды на 4 апреля: штормовой ветер, дождь, гроза ожидаются в Казахстане
-
2577
-
1
-
4
-
-
10👮♀️ В МВД подтвердили информацию об уголовном деле против сына Нурлана Нигматулина
-
2605
-
0
-
25
-